Suite for automated generation of predictive controllers for industrial embedded systems
- Principal Investigator
- Daniel Limón Marruedo
- Funded by
- Programa Estatal de I+D+i
One of the challenges in modern industry is to find ways of improving the efficiency and safety of the manufacturing, chemical and operational processes. Improvements in these aspects result in many different benefits, including energy and raw materials savings, competitive advantages, and security. One of the ways to improve industrial processes is to improve how they are controlled. Currently, most industrial processes are either manually controlled by the workers, who supervise and make adjustments based on their past experience, know-how and the manufacturer’s indications; or controlled using simple low-level control loops. By far, the most commonly used control loop in the industry is based on the well known proportional integral derivative (PID) controllers (Åström & Hägglund, 2009), which have been used for decades. One of the advantages of these controllers is that they are very simple to implement, since they require insignificant computational and memory resources, thus being implementable in any industrial control system. Furthermore, they do not require a model of the system and there exist heuristic techniques for tuning them. In particular, the most common control system used in the industry are devices known as programmable logic controllers (PLC), which are ruggedized digital computers that have been adapted for the control of manufacturing and chemical processes. They are highly reliable, easy to program and designed to withstand the harsh environments that often occur in the industry (high temperatures, vibrations etc.). However, they are also characterized for having small memory and computational resources, mainly due to the fact that they are used for implementing simple control loops and automatons, such as the previously mentioned PID controllers. Consequently, the demand for more powerful PLC devices is small.
While PID controllers and simple automatons are capable of satisfying many of the industrial control needs, significant advantages can be obtained from using more advanced controllers. In particular, one of the most successful and currently researched advanced control strategies is model predictive control (MPC) (Rawlings et al., 2017). MPC uses a model of the system, referred to as the prediction model, to find the “best” possible way in which it could be manipulated during a future time interval, where “best” is defined by some given criterion. That is, from a layman’s perspective, MPC answers the question, “What is the best possible sequence of future actions I could apply to the system during the following X seconds/minutes/hours/etc in order to meet my needs?”. Thus, the implementation of an MPC controller can have a significant impact on the efficiency of the system under a proper selection of the criterion for “best”. Furthermore, one of the properties of MPC that makes it particularly attractive for the industry is that it can explicitly consider constraints when controlling the system. That is, it will find the best possible future sequence of actions, for the given criterion, that satisfies the system’s constraints. This allows for the explicit consideration of safety limits that the MPC controller will take into account. PID controllers and other simple control formulations, on the other hand, do not explicitly consider system constraints. 3 de 35
In spite of its benefits, there are two aspects of MPC that have historically hindered its widespread use in the industry. The first one is the fact that it requires a reliable model of the system, which in many cases can be difficult to obtain. Current trends in the industry, however, may alleviate this issue thanks to the appearance of the so-called digital twins.
The appearance of digital twins is possible thanks to another major trend of the current industrial revolution: the ever increasing availability of data and new algorithms able to analyze it. This plays a key role in the development of reliable models, which can be tuned and validated using available past data of the real system. The growing interest in digital twins, along with the steadily increasing availability of data, has a huge potential to impact in facilitating the implementation of MPC in the industry. The second aspect that has historically hindered the use of MPC in the industry is the fact that MPC requires solving an optimization problem sampling time T. This can be challenging to accomplish, especially if T is small and if we wish to implement the controller in the low-resource control systems typically used in the industry, such as PLCs. In spite of these drawbacks, the advantages of MPC have made it one of the most successful advanced control techniques in the process industry for the last 40 years, particularly so in the petrochemical industry.
One of the main hypotheses of this project is that the current increasing availability of data and use of digital twins, along with recent academic advancements in the field of optimization and automatic code generation, offers the opportunity of expanding the use of MPC in the industry. This is already starting to become a reality, with MPC starting to become more prevalent in some industries, such as in the automotive sector or in renewable energies (wind turbines, solar panels, etc.). In spite of this, there are still many industries and sectors which do not make use of more advanced control techniques, either because of their reluctance to change the way they currently operate, particularly so when substituting the current well known control loops for more advanced control architectures which they barely understand, or because of their reluctance to invest in buying devices with the resources required to be able to solve the MPC’s optimization problem in real-time.
The benefits of being able to implement MPC in the low-resource control systems currently used in the industry, mainly PLCs, to substitute the PID controller currently used for the low-level control loops could have a huge economic impact, as well as provide security improvements. The main objective of this project is to develop a tool that can be used by a wide spectrum of industries to improve the way in which they currently operate their processes by providing a streamlined and intuitive approach for generating MPC controllers that are readily implementable in their current control infrastructure. The target user of SPCIES is an engineering company or department who can benefit from upgrading their controllers in a fast, reliable and inexpensive way.
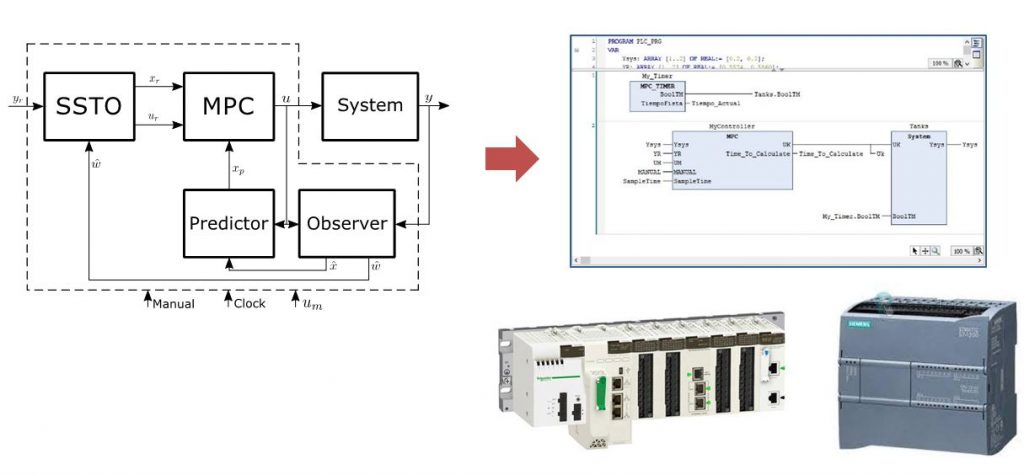
