The Catalytic Synthesis Laboratory is specially-designed to test high-pressure heterogeneous catalytic reactions. The installation is configured in such a way to make it possible to use both gaseous and liquid reactants, which allows for the study of many reactions. The laboratory has five reactors in total: four at laboratory scale, three of which are tubular reactors and the other a slurry reactor, and also a bench-scale tubular reactor. The bench-scale reactor is configured to study the effect of gas recycle.
To date, the Catalytic Synthesis Laboratory has been used to study the following catalytic reactions: ethanol synthesis with oxo synthesis catalysts, hydrodesulphurization, methanol and modified Fisher Trops, hydrogenation of methyl acetate, carbonylation of dimethyl ether, butanol synthesis from ethanol and steam methane reforming.
The main applications given by the laboratory in the study of these catalytic reactions are:
- Characterization of multiple catalysts (screening)
- Experimental design for optimization of operating conditions
- Extensive testing to determine the stability of the catalysts
- Development of kinetic models
- Effect of the gas recycle (at bench-scale)
The following links provide detailed information about the equipment that the laboratory consists of:
A medium pressure fixed-bed reactor
Two high pressure fixed-bed reactors
A high pressure three-phase reactor (Slurry)
A bench-scale plant
Four gas Chromatographs
Medium pressure fixed bed reactor
This system consists of a fixed-bed tubular reactor made of 310 stainless steel, which is 0.9 cm in exterior diameter and 33 cm long, capable of operating at up to 100 bars. The grade 310 stainless steel can withstand temperatures of up to 1100 ºC and shows excellent resistance in corrosive chemical environments such as those due to alcohols and organic acids. To control the reaction temperature, there is an oven capable of reaching 800ºC and an air-conditioning system.
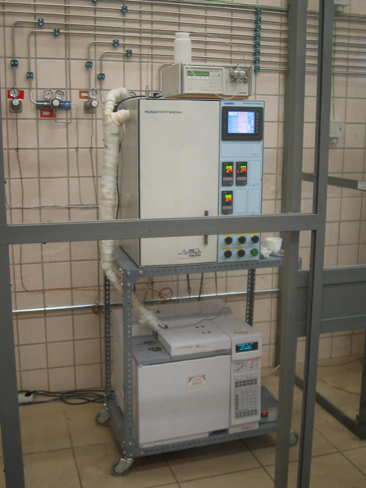
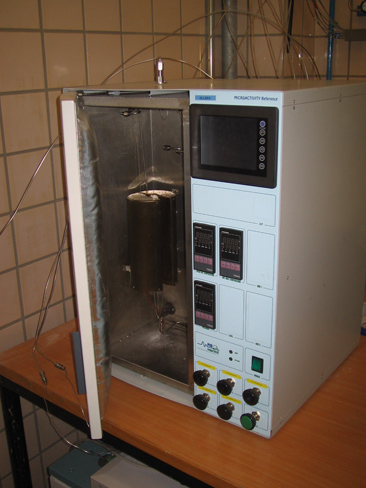
High pressure fixed-bed reactors (HP1 y HP2)
HP1
This system consists of a fixed-bed tubular reactor made of 304 stainless steel, which is 0.9 cm in external diameter and 32.5 cm long, capable of operating at up to 200 bars. To control and measure the temperature it has two resistors which surround the reactor and a thermocouple which measures the axial temperature at three points in the reactor.
HP2
This system consists of a fixed-bed tubular reactor made of 310 stainless steel, which is 1.8 cm in external diameter and 33 cm long, capable of operating at up to 200 bars. The 310 stainless steel can withstand temperature of up to 1100 ºC and shows excellent resistance in corrosive chemical environments. To control the reaction temperature there is an oven capable of reaching 1100 ºC.
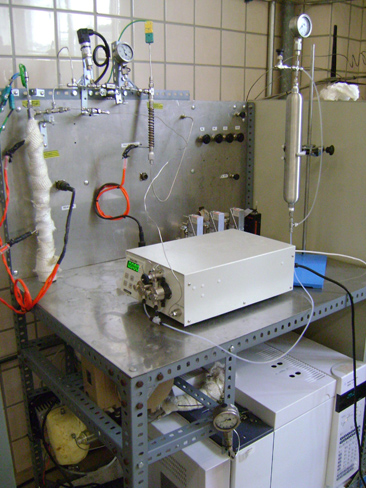
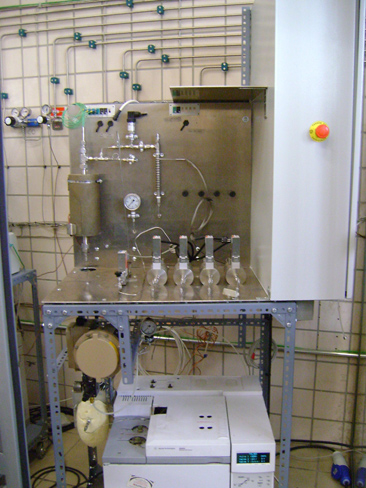
High pressure three-phase reactor (slurry)
This reactor is comprised of a container provided by Autoclave Engineers made of 316 stainless steel (one liter capacity) capable of operating at up to 250 bars. The catalyst remains suspended in the liquid-phase while syngas is sparged in the bottom of the reactor. The liquid is usually a heavy hydrocarbon (enough to not evaporate at reaction temperature) which is water-cooled using a coil located inside the reactor.
The main advantages of this type of reactor are its high heat transfer rate, which leads to optimum control of the reaction temperature, and continuous replacement/regeneration of the catalyst.
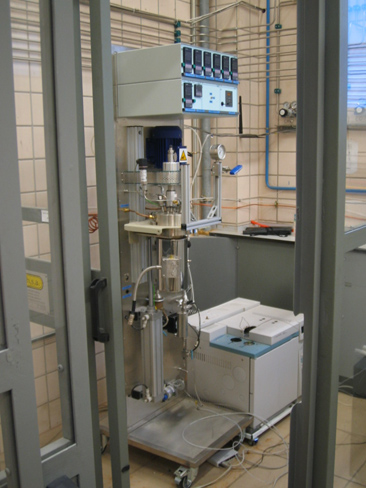
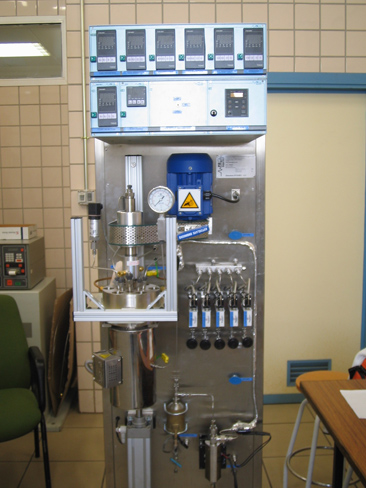
Bench-scale plant
This installation consists of a fixed-bed tubular reactor made of SS 304, 3/4” DN SCH-80 stainless steel, which is 152 cm long and capable of withstanding working pressures of up to 200 bars. The plant has been designed to be portable so that in the future it may be moved near industrial gasifiers where it could take a proportion of the synthesis gas.
The plant has a synthesis gas feed system, a gas purification system, two compressors, (one of which is two-stage to raise gas pressure to reaction pressure, and the other a single stage one for gas recycling), two flow valves for pressure control in the plant, a gas chromatograph to analyze the reaction samples and a condenser for the collection and separation of the synthesized liquids. The control system is composed of an automaton (PLC) with control loops of temperature, pressure and mass flow of gas.
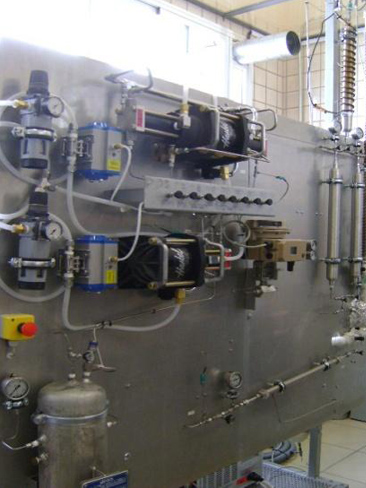
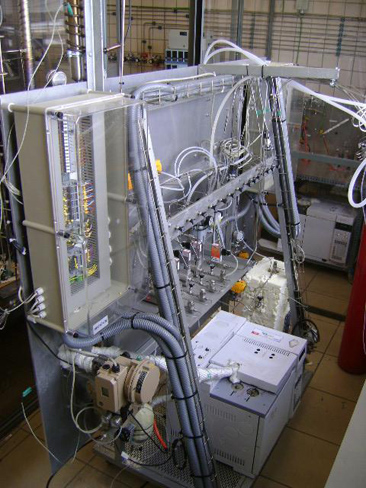
Gas Chromatographs
Each reactor has an associated chromatograph analytic system. In total, the Catalytic Synthesis Laboratory has two Agilent 6890 N Network GC System gas chromatographs and two Agilent 7890 N Network GC System gas chromatographs.
The GC-6890 is equipped with a double injector, two packed columns, a capillary column, a thermal conductivity detector (TCD) and a flame ionization detector (FID).
The GC-7890 also is equipped with a double injector, five capillary columns, a thermal conductivity detector (TCD) and a flame ionization detector (FID).
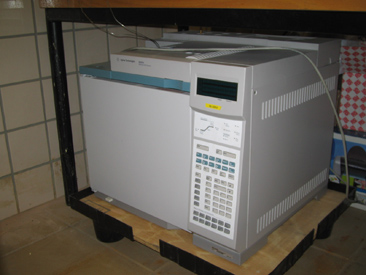
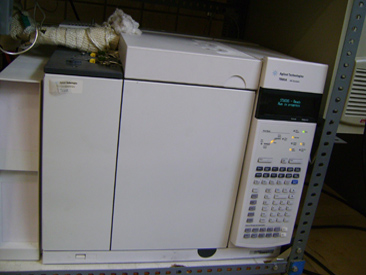